The PDCA Cycle and its Integration in ISO 9001 and ISO 13485
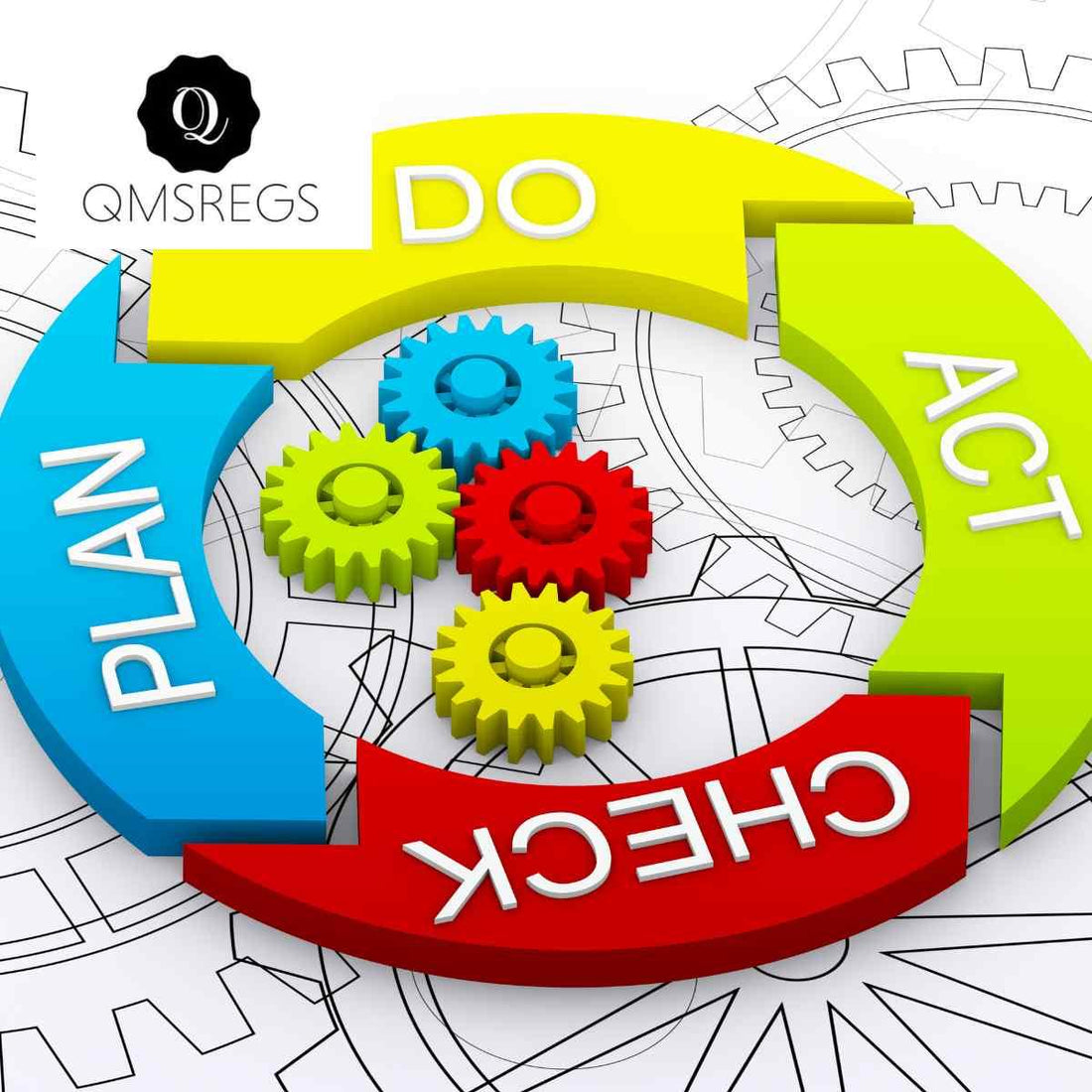
Share
The PDCA (Plan-Do-Check-Act) cycle, also known as the Deming Cycle, is a fundamental concept in quality management and continuous improvement. This iterative four-step management method is used for the control and continuous improvement of processes and products. PDCA is an essential tool within various quality management standards, including ISO 9001 and ISO 13485. This article delves into the PDCA cycle, its incorporation in these ISO standards, and how QMSREGS templates can facilitate effective quality assurance practices, providing a cost-effective solution for organizations.

Understanding the PDCA Cycle
Plan
In the planning phase, the objectives and processes necessary to deliver results in accordance with the expected output (the target or goals) are established. This step involves:
- Identifying and analyzing the problem or opportunity.
- Developing hypotheses about what the issues might be.
- Establishing objectives and processes required to deliver the desired results.
Do
The Do phase is about implementing the plan and testing the solution. This step involves:
- Executing the plan.
- Implementing the process.
- Making the product.
- Collecting data for analysis in the next step.
Check
In the Check phase, the data and results gathered from the Do phase are evaluated. This step involves:
- Comparing the results against the expected outcomes to ascertain any differences.
- Looking for deviations from the plan.
- Understanding the successes and failures.
Act
The Act phase involves taking action based on the results from the Check phase. If the check shows that the plan worked as intended, the changes can be implemented on a larger scale. If not, the cycle starts again. This step involves:
- Implementing the successful plan.
- Identifying further improvements.
- Making adjustments as necessary.
Example of PDCA Cycle in a Manufacturing Company
To illustrate the PDCA cycle, let’s consider a manufacturing company that produces electronic devices. The company has been experiencing an increase in defective products, leading to customer complaints and returns. The company decides to use the PDCA cycle to address this issue.
Plan
Objective: Reduce the defect rate of electronic devices by 20% within six months.
Steps:
- Identify the problem: The defect rate of the electronic devices is high.
- Analyze the root cause: Through data analysis and brainstorming sessions, the team discovers that the main causes of defects are improper assembly processes and substandard components from one of the suppliers.
- Develop a hypothesis: By improving the assembly process and ensuring higher quality components from suppliers, the defect rate can be reduced.
-
Plan the actions:
- Train assembly line workers on the proper assembly techniques.
- Implement a more rigorous inspection process for incoming components.
- Establish a feedback loop with the supplier to ensure component quality.
Do
Implementation:
- Conduct training sessions for assembly line workers.
- Set up an enhanced inspection process for incoming components.
- Work closely with the supplier to address quality issues and improve component standards.
- Pilot these changes on one production line to monitor the impact.
Check
Evaluate the Results:
- Collect data on the defect rate from the pilot production line.
- Compare the defect rate before and after implementing the changes.
- Gather feedback from workers and quality inspectors on the new processes.
Results:
- The defect rate on the pilot line decreased by 25%.
- Workers reported that the new assembly techniques were more effective.
- The supplier provided higher quality components, reducing issues related to substandard parts.
Act
Standardize and Implement:
- Standardize the new assembly techniques across all production lines.
- Continue the rigorous inspection process for all incoming components.
- Maintain regular communication with the supplier to ensure ongoing quality improvement.
- Monitor the defect rate across all production lines to ensure sustained improvement.
Further Actions:
- Document the improved processes and create a quality manual for future training.
- Conduct periodic reviews and audits to ensure the processes are followed.
- Identify other areas of improvement and apply the PDCA cycle as necessary.
By following the PDCA cycle, the manufacturing company was able to systematically identify and address the root causes of defects, leading to a significant reduction in the defect rate and improved customer satisfaction.
Incorporation of PDCA in ISO 9001 and ISO 13485
ISO 9001: Quality Management Systems

ISO 9001 is the international standard that specifies requirements for a quality management system (QMS). Organizations use the standard to demonstrate the ability to consistently provide products and services that meet customer and regulatory requirements. The PDCA cycle is central to ISO 9001, ensuring that quality management processes are continually reviewed and improved.
ISO 13485: Medical Devices

ISO 13485 specifies requirements for a QMS where an organization needs to demonstrate its ability to provide medical devices and related services that consistently meet customer and regulatory requirements. Like ISO 9001, ISO 13485 heavily relies on the PDCA cycle to maintain and enhance the effectiveness of the QMS, ensuring the safety and performance of medical devices.
Utilizing QMSREGS Templates for Effective Quality Assurance
Implementing and maintaining ISO 9001 and ISO 13485 can be a complex and resource-intensive process. This is where QMSREGS templates come into play. QMSREGS offers a range of templates designed to help organizations streamline the implementation of their QMS, ensuring compliance with ISO standards.
Benefits of QMSREGS Templates
- Comprehensive Coverage: The templates cover all necessary aspects of the QMS, from document control and risk management to internal audits and corrective actions.
- Time Efficiency: By using pre-made templates, organizations can significantly reduce the time required to develop and implement their QMS.
- Cost-Effectiveness: Developing a QMS from scratch can be costly. QMSREGS templates provide a cost-effective solution by offering ready-to-use documents that require minimal customization.
- Expertly Crafted: The templates are created by industry experts, ensuring that they meet the latest standards and best practices.
- Ease of Use: Designed to be user-friendly, the templates can be easily adapted to suit the specific needs of an organization.
QMSREGS Templates for ISO 9001 and ISO 13485
Conclusion
The PDCA cycle is a powerful tool for achieving continuous improvement and is a cornerstone of both ISO 9001 and ISO 13485 standards. By integrating the PDCA cycle, organizations can ensure systematic and consistent quality management processes. Utilizing QMSREGS templates can further enhance this process, offering a practical, efficient, and cost-effective solution for implementing robust quality management systems. These templates not only save time and resources but also ensure compliance with international standards, paving the way for superior quality assurance practices.
For more information, you can explore the following resources: